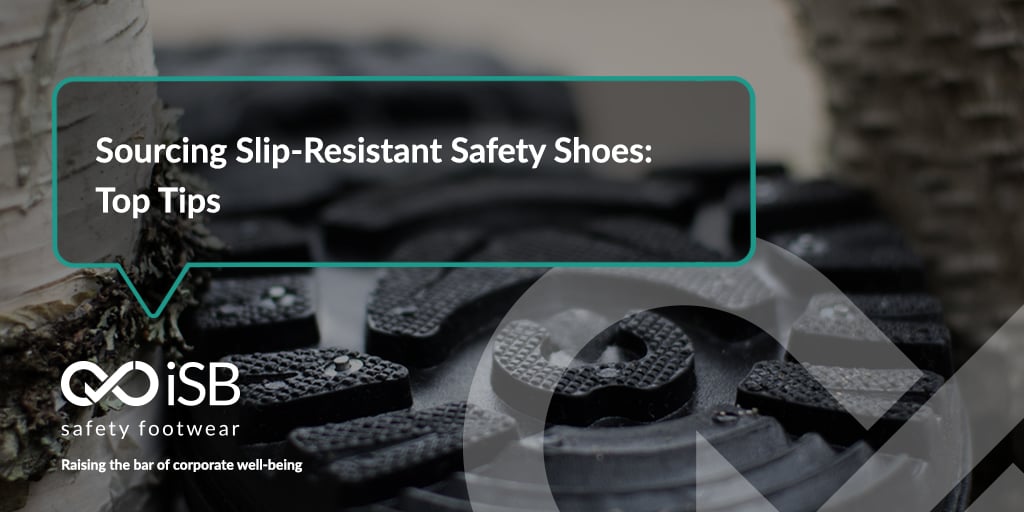
The truth is that the only way to be sure whether footwear is appropriate is to properly test it in your environment. There are, however, a few rules:
- If your employees are working indoors and/or dealing with fluid spills, then buy boots with a softer sole and close-packed tread pattern. For outdoor work or solid contaminants (dust, etc), go for a more open pattern and harder sole.
- Oil-resistant is not the same thing as slip-resistant. It refers to how well the footwear stands up to potential damage from oil. However, oil-resistance can slow the wear of soles in certain environments so you may want to look at footwear that is both oil- and slip-resistant.
- The cheapest footwear is generally not the best.
- Footwear your employees resist wearing will not do the job. Make sure that footwear looks attractive, fits well, and is comfortable. Talking to your employees is always beneficial. Some people, for example, prefer boots, whilst others really don’t and are likely to take them off when not in view.
When selecting footwear, start with a risk assessment. Look at your environment and work out what kind of contaminants might cause a slipping hazard. Consider outdoor versus indoor work and your climate (for example, black ice is more of a worry in places where the temperature tends to dip below freezing then come back above multiple times). Then contact the supplier and talk to them about your needs. You can often ask for testing for your specific environment, but the best thing to do is request trial pairs that can then be tested by experienced employees over a longer period of time.
Never rely entirely on lab reports or descriptions, but do your own testing over time. Look for shoes designed for your specific environment. For example, the kind of shoes that are good for warehouse employees who have to keep going outside in rain or snow are not the same as those for restaurant workers (food spills can clog the tread of some designs, negating the slip-resistant qualities).
Remember that no one shoe or boot eliminates all risks. Outdoor workers, for example, may need different footwear in winter and summer – and, of course, temperature differences can affect comfort. It is quite common and good practice to purchase a separate pair of safety footwear for the winter. Waterproof, thermal boots are highly recommended for this time of year.
Finally, consider durability and wear. Slip-resistant footwear will inevitably lose its grip over time. Choose footwear that has good reviews for durability or has been tested using a test such as the SATRA Pedatron Test. Slip-resistant footwear also needs to be cleaned regularly to prevent the soles from becoming clogged – set guidelines to ensure this happens. You also need a system for detecting worn footwear and replacing it before it becomes ineffective.
Ultimately, though, the most important consideration is to purchase footwear that is properly tested for your specific needs – and that means knowing exactly what those needs are through a thorough risk assessment before buying your footwear. If you are looking for high-quality slip-resistant work shoes and boots, contact iSB Group today to find out how our managed PPE solutions can help you.
You Might Like...
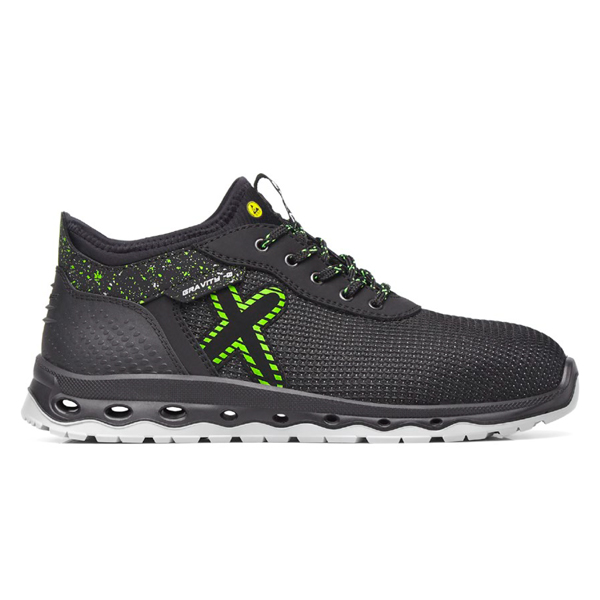
Gravity Jupiter Safety Trainers- E3200
Ultra resistant textile TECNO-TEXT upper
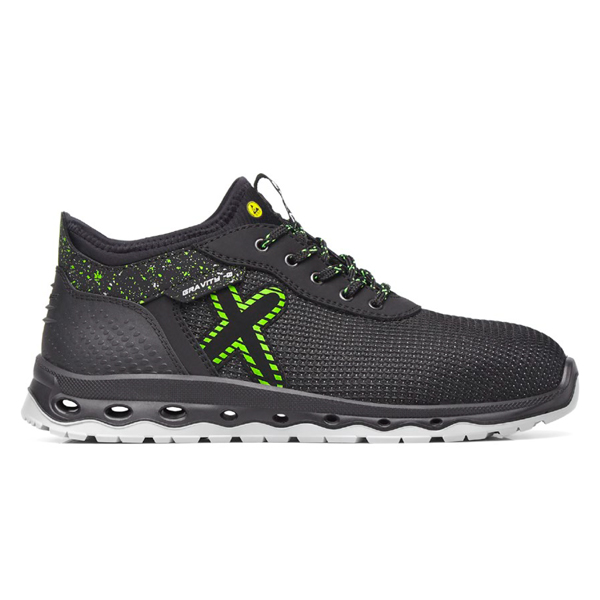
Gravity Jupiter Safety Trainers- E3200
Ultra resistant textile TECNO-TEXT upper
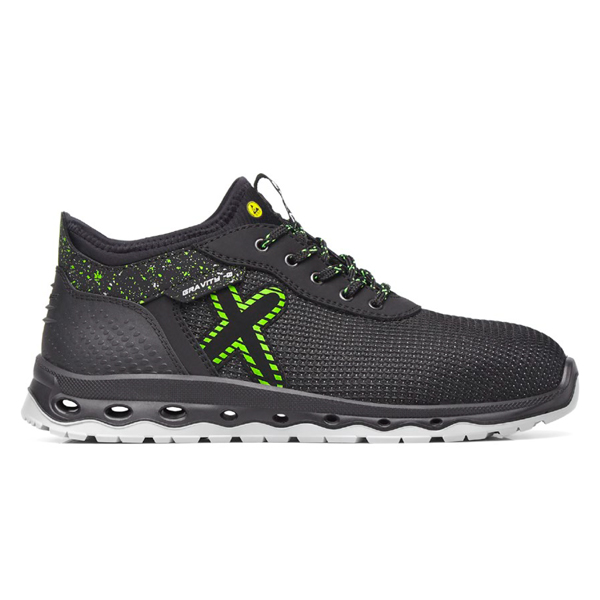
Gravity Jupiter Safety Trainers- E3200
Ultra resistant textile TECNO-TEXT upper
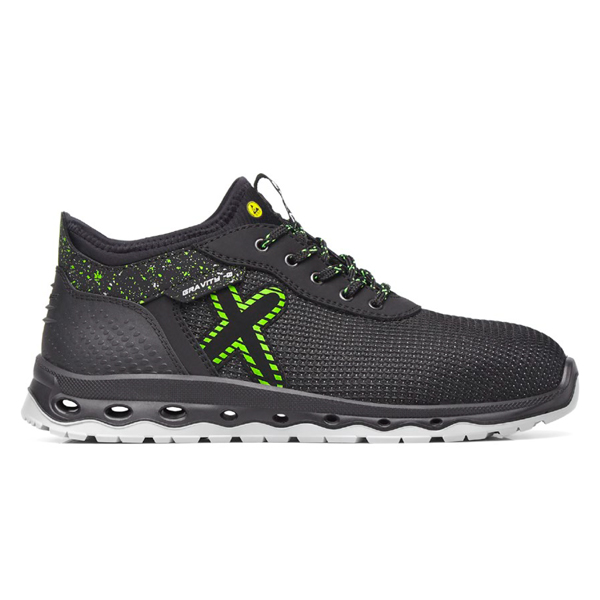
Gravity Jupiter Safety Trainers- E3200
Ultra resistant textile TECNO-TEXT upper