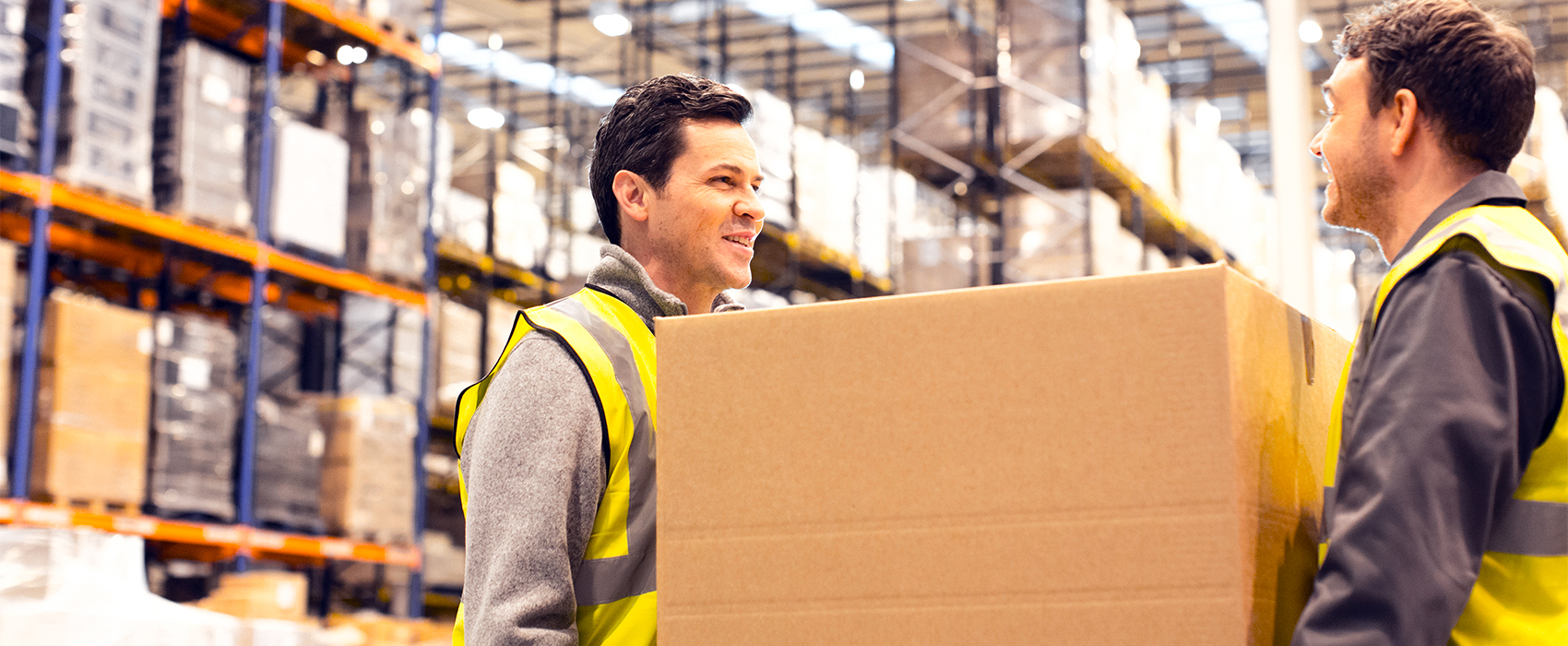
Manual handling operations regulations 1992
The Manual Handling Operations Regulations 1992 contain the legal obligations employers must meet concerning manual handling at work. A vital part of health and safety law in the UK, they are designed to protect employees from being injured or suffering ill health as a result of their work.
The most recent UK Labour Force Survey estimates work-related musculoskeletal disorders including those caused by manual handling account for around a quarter of all working days lost due to work-related ill health. The Manual Handling Operations Regulations 1992 contain detailed information to help businesses assess and reduce the risk of their employees being injured during manual handling operations in their workplace.
What is manual handling?
Manual handling activities are those involving the transport or support of loads, including the lifting, lowering, pushing, pulling, carrying and moving of those loads.
Manual Handling Operations Regulations 1992: the basics
The Manual Handling Operations Regulations 1992 require employers to avoid, assess and reduce the risk of manual handling injuries resulting from their workplace activities.
The law sets out a hierarchy of priorities employers must follow.
In order of importance, these are: Avoid, Assess, Reduce
- AVOID so far as is ‘reasonably practicable’, avoid the need for employees to undertake manual handling operations at work that risk them being injured. This might require redesigning a task to avoid the need to move a load, or through mechanisation or automation.
Where manual handling operations cannot be avoided:
- ASSESS the risk of injury, taking into account the nature of the task, the properties of the load, the work environment and conditions, and psychosocial risk factors such as high workloads, tight deadlines and a lack of control over work and working methods. This assessment should also consider the physical suitability of the employee to carry out the planned task; the clothing, footwear and PPE he or she is wearing; that person’s knowledge and training; and any other relevant risk factors relating to individual capability.
- REDUCE the likelihood of injury to its lowest possible level by taking ‘reasonably practicable’ actions to control the risk. This might entail providing mechanical assistance such as a hoist or sack trolley, or changing the task, load or an element of the working environment to reduce the risk. Where it is possible to do, general indications on the weight and weight distribution of loads may also be given.
In this context, the term ‘reasonably practicable’ entails balancing the level of risk against the financial cost, investment of time, or other difficulty of taking measures to control that risk.
Manual Handling Operations Regulations 1992: Further guidance
In addition to complying with the regulations, the Health and Safety Executive recommends employers encourage early reporting of symptoms by their employees that may be related to manual handling, recognising that reducing manual handling injuries at work requires collective effort.
Your employees are an important asset – they know the risks at work and, as such, are well placed to offer suggestions for solutions to reduce or eliminate them. This includes any specific difficulties caused by the size, shape or weight of loads; how often loads are handled; the order of tasks; or the working environment, such as space constraints, uneven flooring and unsuitable shelving or storage systems.
Some useful links
The full Manual Handling Operations Regulations 1992 contain detailed advice on how to assess the risk of manual handling injuries at work and actions that may be taken to control the risk, including information on proper lifting technique.
The HSE website also has further guidance and training materials.
iSB Group have been established 48 years and are trusted partners to some of the largest 3PLs and distributors in the UK. Our range of health and safety products is extensive, contact the team to discuss or review the range here.
You might also like
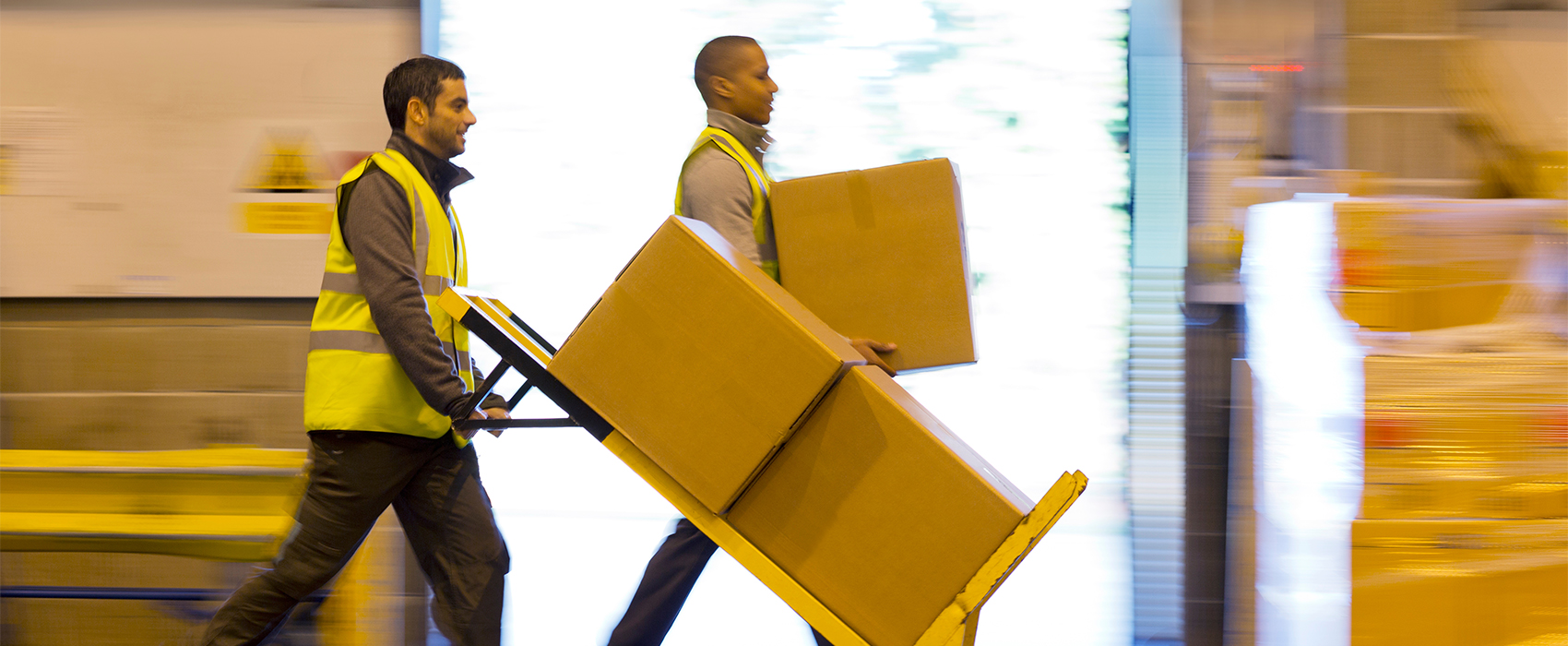
Safe lifting techniques in the workplace
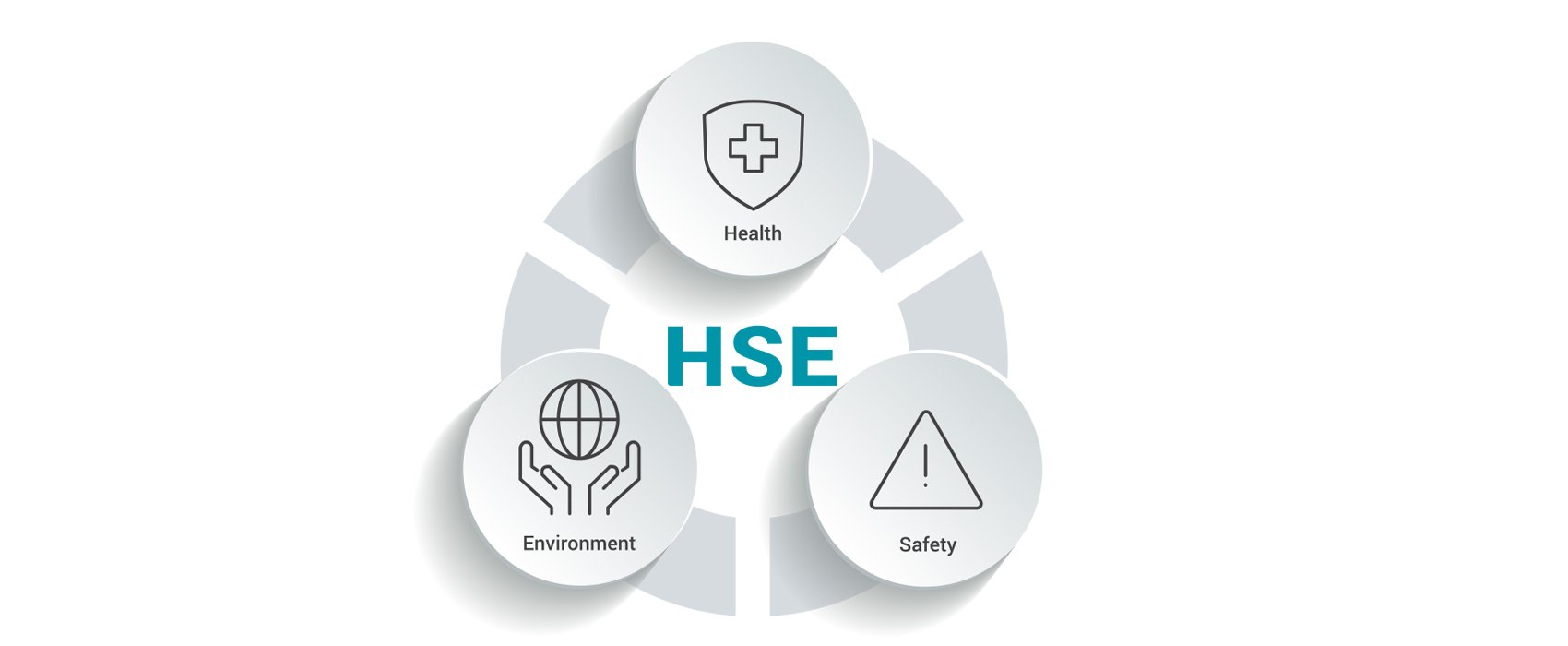