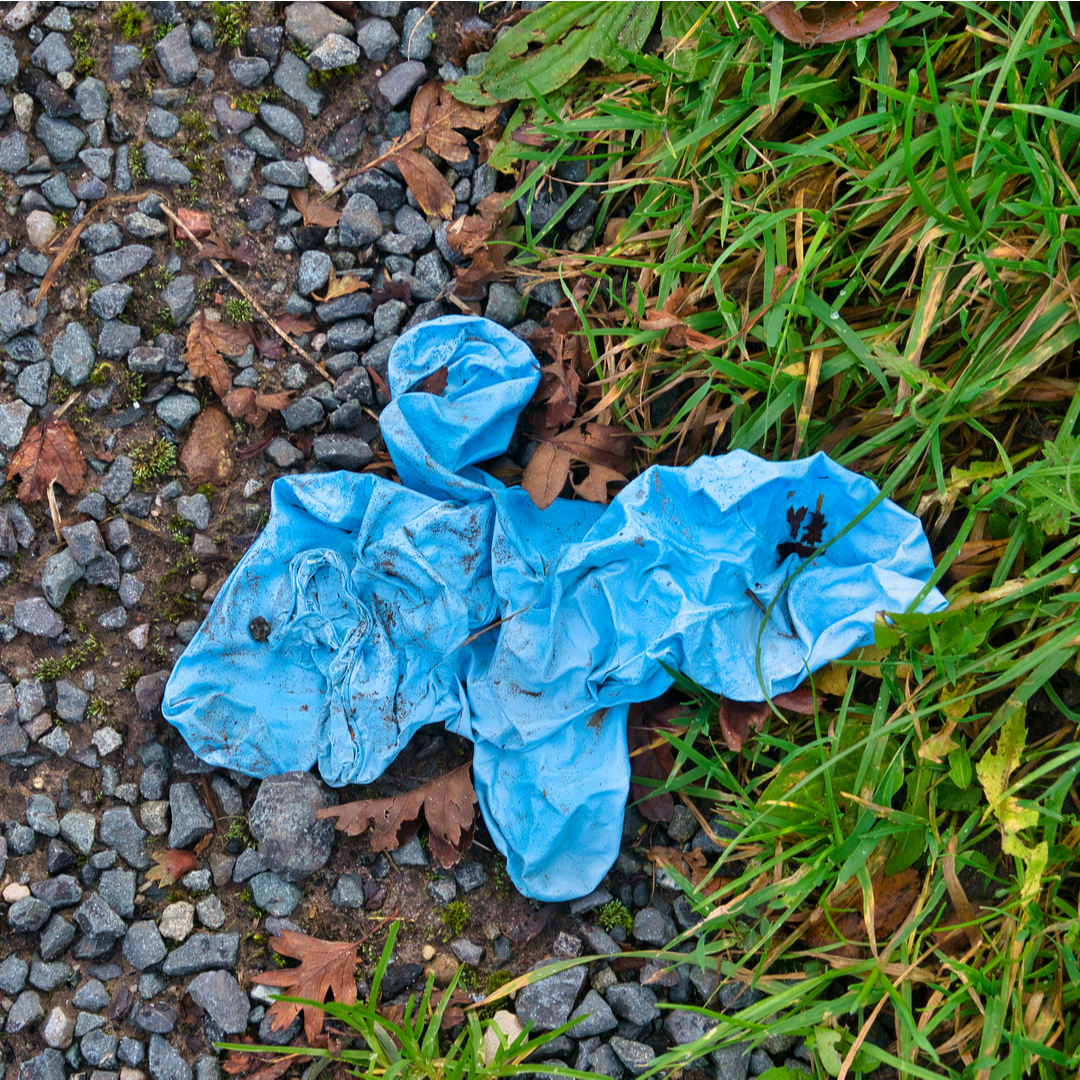
In many instances, it has also made us care more about our planet.
Few of us can fail to have been shocked by the images of disposable face masks, gloves and wipes littering our streets and green spaces, and polluting our waterways, causing a hazard to wildlife and creating an eyesore.
PPE has been essential for preventing the spread of COVID-19, but nobody could have imagined just how much of it would be required, for how long, and what a blow it would be to the drive for a circular economy.
As we begin to try to emerge from the shadow of the pandemic, we are increasingly speaking to businesses keen to improve their sustainability credentials by reducing the amount of waste they produce, and are collaborating with our suppliers to offer workable solutions.
Here, we break down some small changes that can help make a difference.
Increasing the lifespan of Safety Gloves
We’ve blogged before about how preventing the spread of germs needn’t mean going full-on disposable. Good quality work gloves can not only be washed and re-worn, but can also be used alongside hand sanitiser during these times of heightened awareness to potential germ-transfer.
A higher-quality glove will also last longer.
Our tip: Avoid white or other light-coloured gloves, which are prone to staining, making them look dirty and increasing the chance of them being thrown away when they are still safe to wear. Opt instead for a darker colour, and encourage your employees to wash and re-use their gloves.
Guarding against a throw-away mindset
Many of our clients are trialling solutions to help reduce the likelihood of workers throwing away gloves and other items of PPE that are still able to be worn safely and comfortably, on the basis that they look dirty or worn.
Manual and technology-monitored allocation systems, whereby individual workers are given a limited amount of safety workwear items to last for an agreed period of time, may work for some organisations, but are most effective when combined with education for employees on how to care for and maintain their safety workwear, and the reasons for doing so.
Choosing sustainable or longer-lasting alternatives
In many instances, choosing alternative products can help to reduce wastage, as those products either last longer or create less impact on the environment in their production and disposal. Some of these alternatives may be more expensive at point of purchase, but businesses will reap the rewards further down the line in terms of increased longevity, as well as improved sustainability credentials.
As an example, many logistics companies have been able to reduce waste whilst also keeping their employees safer, by providing workers in the returns and rework space with an alternative type of knife to cut open packages.
The Slice range of safety cutters have advanced ceramic blades, which last up to 11 times longer than traditional exposed steel blades, do not rust, and are recyclable after use. What’s more, they cut with their hardness rather than their sharpness, dramatically reducing the risk of injury.
Working in partnership
At iSB Group, we are committed to helping logistics companies to achieve their goals, and work with clients to help them find solutions to their needs that are as safe and effective as they can possibly be. This includes proactively helping to source more sustainable products, and liaising with customers to come up with creative ways of reducing waste.
Talk to our team about how we could help your business reduce waste and drive sustainability while improving safety. Give us a call on 0121 749 4433 or email sales@isb-uk.com.
You Might Like...
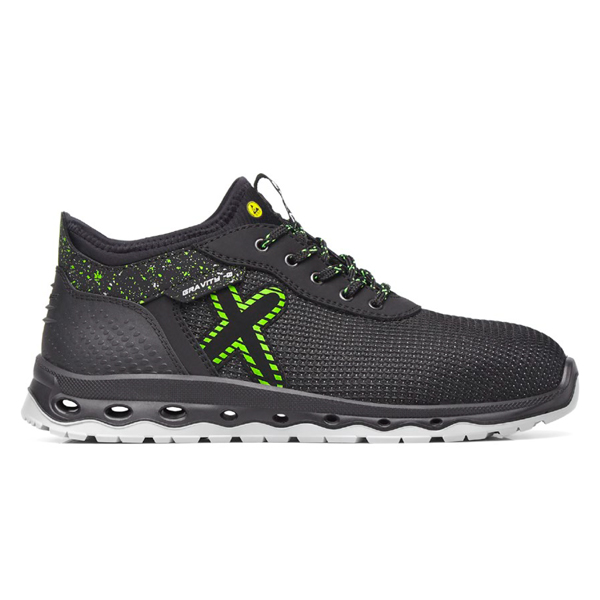
Gravity Jupiter Safety Trainers- E3200
Ultra resistant textile TECNO-TEXT upper
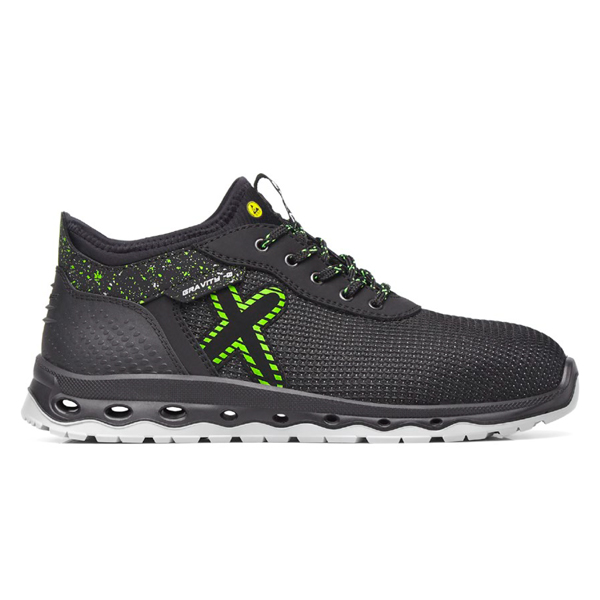
Gravity Jupiter Safety Trainers- E3200
Ultra resistant textile TECNO-TEXT upper
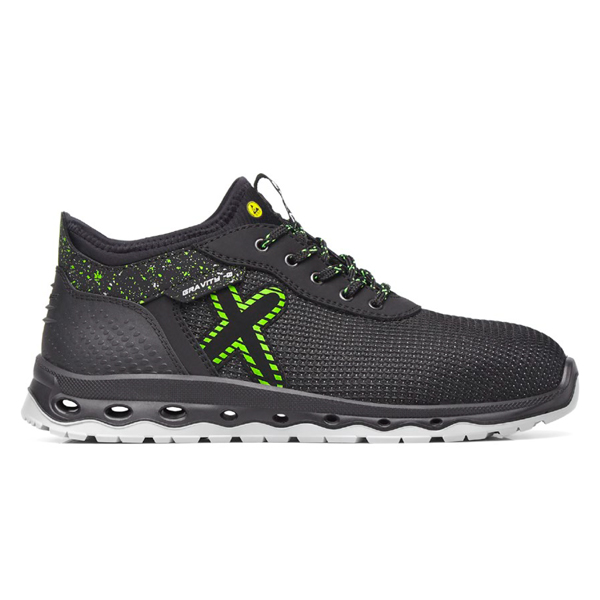
Gravity Jupiter Safety Trainers- E3200
Ultra resistant textile TECNO-TEXT upper
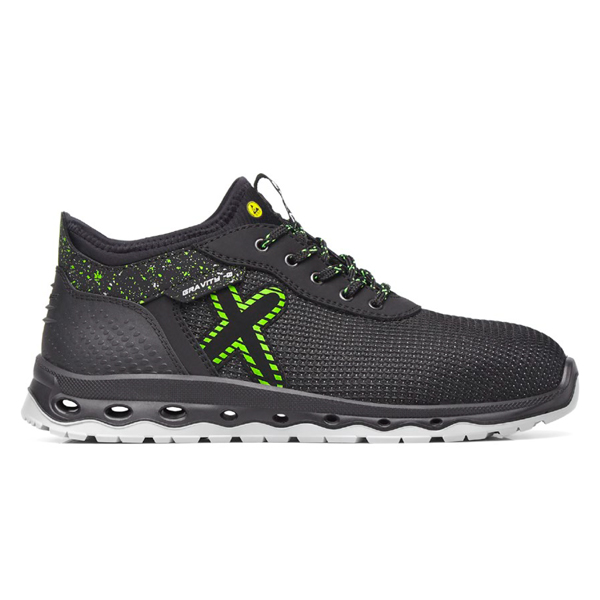
Gravity Jupiter Safety Trainers- E3200
Ultra resistant textile TECNO-TEXT upper